Delving into the realm of fork and blade connecting rods, this article embarks on a journey to unravel their intricate design, explore their manufacturing processes, and showcase their diverse applications. From their unique shape and dimensions to the materials employed in their construction, we delve into the fascinating world of these essential engine components.
The fork and blade connecting rods play a pivotal role in the smooth operation of internal combustion engines. Their design and manufacturing processes are meticulously engineered to withstand the immense forces and stresses encountered during engine operation, ensuring optimal performance and longevity.
Design Characteristics
Fork and blade connecting rods are essential components of an engine, responsible for transmitting power from the piston to the crankshaft. These rods are meticulously engineered to withstand the extreme forces and stresses encountered during engine operation, and their design characteristics play a crucial role in their performance and durability.
Fork and blade connecting rods are typically constructed from high-strength materials such as forged steel or aluminum alloys. Steel provides exceptional strength and durability, while aluminum alloys offer a lighter weight and better heat dissipation. The shape and dimensions of the connecting rods are carefully designed to optimize their strength, rigidity, and weight.
Shape and Dimensions
Fork connecting rods feature a forked design at the piston end, which allows for direct attachment to the piston pin. The blade connecting rods, on the other hand, have a flat, blade-like shape at the piston end, which connects to the piston via a wrist pin.
The shape of the connecting rods influences their strength and rigidity under various loading conditions.
The length of the connecting rod is also a critical design parameter. A longer connecting rod reduces the side thrust on the cylinder walls, but it also increases the overall engine height. Shorter connecting rods, while reducing engine height, can increase side thrust and piston acceleration.
Manufacturing Processes
Fork and blade connecting rods are critical components in internal combustion engines, and their manufacturing processes play a vital role in ensuring their performance and reliability.
Various manufacturing techniques are employed to produce these connecting rods, each with its own advantages and disadvantages.
Forging
- Forging is a metalworking process that involves shaping metal by applying high-pressure force. In the case of connecting rods, forging is often used to create the basic shape of the rod.
- The advantages of forging include the ability to produce strong and durable components with a fine grain structure. However, forging can be a relatively expensive process, and it is not suitable for all types of connecting rods.
Casting
- Casting is a process in which molten metal is poured into a mold to create the desired shape. Casting is often used to produce connecting rods with complex shapes or hollow sections.
- The advantages of casting include the ability to produce complex shapes with high precision. However, casting can produce components with a coarser grain structure, which can affect their strength and durability.
Powder Metallurgy, Fork and blade connecting rods
- Powder metallurgy is a process in which metal powders are pressed into the desired shape and then sintered to bond the particles together. Powder metallurgy is often used to produce connecting rods with high strength and wear resistance.
- The advantages of powder metallurgy include the ability to produce components with high precision and a fine grain structure. However, powder metallurgy can be a relatively expensive process, and it is not suitable for all types of connecting rods.
Machining
- Machining is a process in which metal is removed from a workpiece using a cutting tool. Machining is often used to finish the shape of connecting rods and to create precision features such as bearing surfaces.
- The advantages of machining include the ability to produce components with high precision and a smooth surface finish. However, machining can be a relatively slow and expensive process.
Performance Considerations
Fork and blade connecting rods offer distinct performance characteristics that influence their suitability for various applications. The design and manufacturing processes employed significantly impact their performance.
The fork and blade design contributes to improved rigidity and strength, reducing deflection and vibration during engine operation. This enhanced structural integrity allows for higher engine speeds and loads without compromising performance.
Material Selection
- The choice of materials, such as forged steel or lightweight alloys, affects the strength, weight, and durability of the connecting rods.
- High-strength materials, like forged steel, provide excellent load-bearing capacity and durability.
- Lightweight alloys, such as aluminum or titanium, reduce overall engine weight, improving fuel efficiency and performance.
Manufacturing Techniques
- Precision machining and forging processes ensure accurate dimensions and smooth surfaces, minimizing friction and wear.
- Heat treatment strengthens the material, improving its fatigue resistance and overall durability.
- Surface treatments, such as nitriding or shot peening, enhance wear resistance and fatigue life.
Application Examples
- High-performance racing engines utilize fork and blade connecting rods due to their ability to withstand extreme loads and high engine speeds.
- Automotive engines benefit from the improved rigidity and strength of fork and blade connecting rods, allowing for higher engine efficiency and reduced emissions.
- Industrial applications, such as heavy-duty machinery, employ fork and blade connecting rods for their durability and ability to handle high loads and torque.
Failure Analysis
Failure analysis of fork and blade connecting rods is crucial for understanding the causes of failures and implementing preventive measures. Common failure modes include fatigue, wear, corrosion, and overload.
Fork and blade connecting rods play a crucial role in the internal combustion engine, but they can also be used in other applications. For instance, the concept of tuning paste, used to adjust the pitch of drums drums tuned with tuning paste , has been adapted to create innovative designs for fork and blade connecting rods.
These designs enhance engine performance and durability, demonstrating the versatility of this engineering component.
Fatigue Failure
Fatigue failure occurs due to repeated loading and unloading cycles that weaken the material over time. It is a common failure mode in fork and blade connecting rods due to the dynamic nature of their operation. The fatigue strength of the material can be improved by using high-strength materials, reducing stress concentrations, and improving surface finish.
Wear Failure
Wear failure occurs due to the gradual loss of material from the surface of the connecting rod. This can be caused by abrasive wear, adhesive wear, or fretting wear. Wear resistance can be improved by using wear-resistant materials, applying coatings, and ensuring proper lubrication.
Corrosion Failure
Corrosion failure occurs when the connecting rod is exposed to corrosive environments, such as moisture, acids, or salts. Corrosion can weaken the material and lead to premature failure. Corrosion resistance can be improved by using corrosion-resistant materials, applying protective coatings, and ensuring proper maintenance.
Overload Failure
Overload failure occurs when the connecting rod is subjected to excessive loads beyond its design limits. This can cause sudden and catastrophic failure. Overload resistance can be improved by using high-strength materials, ensuring proper design, and avoiding overloading the engine.Failure
analysis techniques for fork and blade connecting rods include visual inspection, microscopic examination, fractography, and stress analysis. These techniques help identify the root cause of failure and guide preventive measures.
Applications
Fork and blade connecting rods find applications in various industries, primarily in reciprocating engines and compressors.
Advantages of Fork and Blade Connecting Rods
- High strength-to-weight ratio, enabling them to withstand high loads and stresses.
- Improved fatigue resistance, making them suitable for applications involving cyclic loading.
- Compact design, allowing for space optimization in engine compartments.
- Reduced friction, minimizing power losses and improving engine efficiency.
Disadvantages of Fork and Blade Connecting Rods
- Higher manufacturing costs compared to traditional connecting rods.
- Limited availability of suitable materials for high-performance applications.
- Potential for noise and vibration due to the unique shape.
Specific Applications
Fork and blade connecting rods are commonly used in:
- Automotive engines, particularly in high-performance and racing applications.
- Diesel engines, where their strength and fatigue resistance are advantageous.
- Compressors, both reciprocating and centrifugal types.
- Hydraulic pumps, where their compact design and reduced friction improve efficiency.
General Inquiries: Fork And Blade Connecting Rods
What are the primary functions of fork and blade connecting rods?
Fork and blade connecting rods serve as the link between the piston and the crankshaft, transmitting the reciprocating motion of the piston into rotary motion of the crankshaft.
What materials are commonly used in the construction of fork and blade connecting rods?
High-strength materials such as forged steel, aluminum alloys, and titanium are commonly employed in the construction of fork and blade connecting rods due to their ability to withstand high loads and stresses.
How do the shape and dimensions of fork and blade connecting rods affect their performance?
The shape and dimensions of fork and blade connecting rods are carefully designed to optimize their strength, weight, and dynamic characteristics, ensuring efficient engine operation.
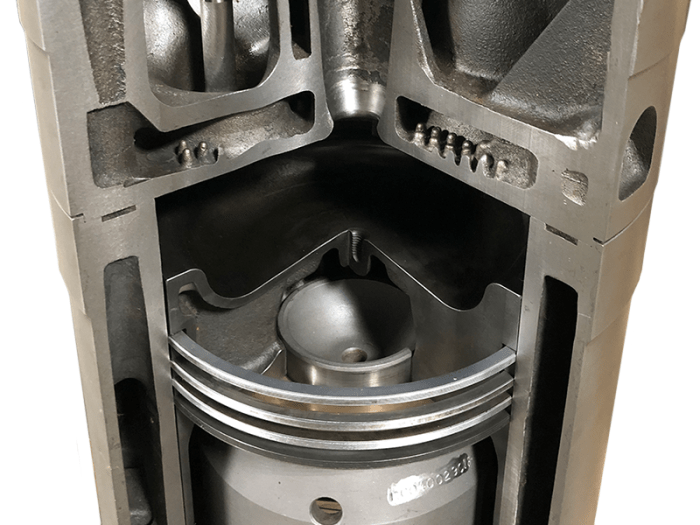